世界經濟論壇發布“燈塔工廠”新名單
- 發布時間:2022-10-12 09:46:46
- 瀏覽量:803
世界經濟論壇宣布11家新工廠加入其全球燈塔網絡——這個由100多家先進生產工廠組成的社區。該社區致力引領第四次工業革命先進技術的應用,以不斷提高生產力及員工參與度,促進可持續發展以及供應鏈韌性。
憑借在減少環境足跡方面的突出表現,四家燈塔工廠被評選為“可持續發展燈塔工廠”。這幾家工廠發揮著全球領導作用,在運營過程中積極釋放第四次工業革命各項技術的潛力,不斷踐行可持續發展承諾并提高運營競爭力。
在全球衰退危機、能源價格不斷攀升,供應鏈運轉中斷的背景下,這些燈塔工廠針對制造業如何保持競爭力并繼續創造就業機會的問題,為商界領袖和政策制定者樹立了榜樣。
最新的全球燈塔網絡包含4家榮膺“可持續燈塔”稱號的工廠:
Arçelik(羅馬尼亞,烏爾米):Arçelik烏爾米綠色工廠,實現了100%綠電供應,成功開展了數個可持續發展用例項目,包括用于能源管理的數字孿生項目以及集成了先進水處理工廠的水資源閉環管理系統。在用水緊張的背景下,該項目為每件產品生產節約25%用水量,降低17%能源消耗以及22%溫室氣體排放。
美光(新加坡):隨著對內存和存儲解決方案的需求不斷增長,新加坡美光科技有限公司需要擴大和增加千兆字節產品的產量,同時減少對環境的影響。2018年到2021年,新加坡美光科技有限公司產量增加了270%,同時每生產千兆字節的資源消耗減少了45%。這得益于可持續的技術發展,通過跟蹤環境足跡不斷優化材料消耗。
聯合利華(印度,達帕達):為了實現企業的可持續發展目標,即到2025年將溫室氣體范圍1和2的排放量減少70%(相較于2015年基線),并在應對產量快速增長的同時減少水資源消耗,聯合利華達帕達開展了14個使用案例,如通過集成能源管理系統實現以機器學習驅動的能源優化,運用數字孿生技術加速制定生態友好型配方生產策略。達帕達將范圍1和2的排放量減少了54%,范圍3的排放量減少了43%,用水量減少了36%,提前實現了其減排目標。
西部數據(中國,上海):在需求不斷增長的情況下,西部數據在2017年至2021年期間將工廠拍字節(PB)產量翻了一番,同時減少了每PB產品的環境足跡,以實現企業的減排目標。這一結果由第四次工業革命的多項科技驅動,如運用機器學習動態優化水循環工廠性能以及根據實時操作數據檢測異常能耗預測系統。這些措施使每PB產品水資源消耗減少了62%,能源消耗減少了51%。
新增的11家燈塔工廠包括:
安捷倫科技(新加坡):為簡化小批量、高復雜度儀器的高科技制造過程,以滿足不斷增長的客戶需求,安捷倫新加坡公司應用了物聯網驅動的數字孿生技術、人工智能和機器人(8.710, 0.25, 2.96%)自動化解決方案以實現可持續增長,克服了專業人力資源上的瓶頸,并將勞動力轉變為掌握第四次工業革命技術的通用可塑性人才。這使得產出增加了80%,生產力提高了60%,周期時間縮短了30%,質量成本降低了20%。
寧德時代(中國,宜賓):為了滿足業務大幅增長和質量提高的預期并實現可持續性發展,寧德時代在宜賓市建立了大型綠色工廠。該工廠在寧德時代總部燈塔數字計劃基礎上,進一步深入應用人工智能、物聯網和柔性自動化技術,生產線速度提高17%,產量損失減少14%以及實現了零碳排放。
西普拉(印度,印多爾):為了在全球范圍內保持高質量、實惠的藥品供應,同時應對材料和勞動力成本的增加,西普拉在印度22個工廠同時部署了數字化、自動化和分析解決方案。印多爾口服固體制劑工廠通過實施30個第四次工業革命技術用例,將總成本降低了26%,質量提高了300%,同時減少了28%的溫室氣體(GHG)排放量,引領了數字轉型之旅。
達能(波蘭,奧波萊):達能奧波萊工廠開啟了數字化轉型,以更好地應對其生產產品的復雜性。工廠通過車間的互聯互通、人工智能與自動化技術的大規模運用,在進一步優化產品質量的同時,成功降低了19%的成本,實現了12%的效率提升,并減少了近50%的溫室氣體排放。該工廠在數字化轉型方面成為達能其他39家歐洲工廠的榜樣,并在波蘭榮獲 “最佳雇主”的稱號。
瑞迪博士(印度,海得拉巴):面對嚴重的價格侵蝕和快速提升的質量預期帶來的業務挑戰,這家有25年歷史的工廠開始了大規模數字化之旅,在仿制藥市場上不斷發展。該工廠通過利用靈活模式,并利用物聯網和民主化平臺進行高級分析,部署了40多個第四次工業革命技術用例。工廠由此將制造成本降低了43%,同時積極主動地提高質量,并將能源消耗減少了41%。
偉創力(巴西,索羅卡巴):為了提高工廠競爭力、可持續性和員工健康水平,偉創力在端到端價值鏈上應用了第四次工業革命技術,例如物聯網驅動的電子廢品回收和供應鏈控制塔。數字化轉型之旅使勞動成本降低50%,材料損耗減少了81%,同時提高了客戶滿意度(+18%)和員工福祉。
海爾(中國,青島):面對日益增長的定制化設計、快速交付和高品質的需求,海爾冰箱工廠借助大數據、數字孿生和先進視覺檢測技術,加快研發、升級制造流程和物流調度模式。訂單響應周期縮短了35%,生產效率提高了35%,質量性能提高了36%。
美的(中國,順德):為了滿足在更短交貨期內交付高質量產品的需求,美的順德工廠在端到端價值鏈中應用了人工智能、數字孿生和其他第四次工業革命技術,使單位生產成本降低24%、交付時間縮短41%、研發時間縮短30%、缺陷率降低51%。
億滋(印度,斯里城):為了保持卓越的批量交付數量,實現成本領先,并在動蕩的環境中進一步增強韌性和多樣性以超越市場,億滋的斯里城工廠開展了端到端的數字化工作、應用預測分析、人工智能和先進的自動化技術,將勞動生產率提高89%、制造成本降低38%,并將女性勞動力維持在50%。該工廠成為了億滋在全球的標桿制造基地。
三一重工(中國,長沙):為應對重工行業市場的周期性波動、多品種小批量(263個品類)及重型部件生產的挑戰,三一重工長沙工廠充分利用柔性自動化生產、人工智能和規?;腎IoT,建立了一個數字化柔性的重型設備制造系統。最終實現工廠產能擴大了123%,生產率提高了98%,單位制造成本降低了29%。
西部數據(中國,上海):為應對250%的年增長率、短期18個月的技術轉型周期以及勞動力挑戰,西部數據上海半導體后端工廠實施了多樣化的第四次工業革命技術,如自動化產品設計系統、基于機器學習的虛擬晶圓測試和智能規劃系統。該工廠將產品上市時間縮短了40%,產品成本降低了62%,生產率提高了221%。
免責聲明:部分文章信息來源于網絡以及網友投稿,本網站只負責對文章進行整理、排版、編輯,意為分享交流傳遞信息,并不意味著贊同其觀點或證實其內容的真實性,如本站文章和轉稿涉及版權等問題,請作者在及時聯系本站,我們會盡快和您對接處理。
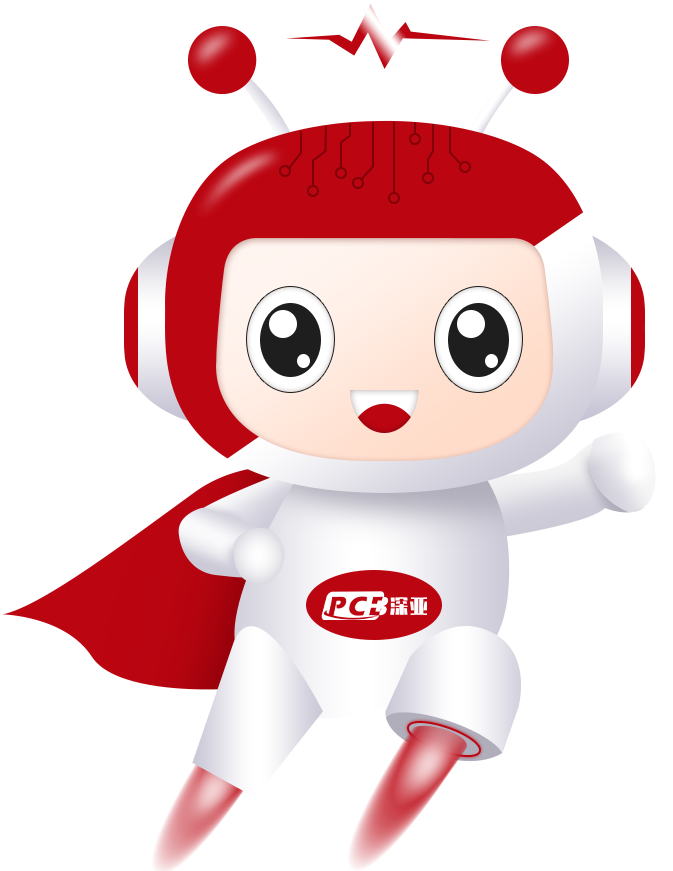