汕頭pcb廠商詳解SMT技術的常識和可制造性設計
- 發布時間:2022-09-15 10:53:49
- 瀏覽量:650
目前,SMT技術非常成熟,廣泛應用于電子產品中。因此,電子產品設計人員有必要了解SMT技術的可制造性(DFM)要求的常識和設計。對于采用SMT技術的產品,在設計之初,應綜合考慮生產工藝、原材料選擇、設備要求、器件布局、測試條件等因素,盡可能縮短設計時間,確保從設計到制造的一次成功。
元器件布局是將元器件按照原理圖的要求和元器件的封裝要求,整齊美觀地排列在PCB上,滿足可制造性、測試性、維護性等方面的要求,滿足電路功能和性能的要求。在設計元件布局時,工藝流程應該最少,可制造性應該是最好的。組件布局設計的基本原則如下:
(1)元件排列均勻,盡量將相似元件排列在同一方向,功能相同的模塊排列在一起;結構相同的電路部分應盡量對稱排列。
(2) 元器件的布局遵循“先難易,先大后小”的布局原則,即重要單元電路和核心元件先布局,其他元件先布局在它周圍。
(3) 相互連接的元件應盡量靠近,以保證最短的布線距離,有利于增加布線密度。
(4) 縮短高頻元件之間的連線,減少它們的分布參數和相互間的電磁干擾。易受干擾的元件應隔離或屏蔽。
(5) 對熱敏元件(溫度檢測元件除外),布線應遠離產生大量熱量的元件。一般發熱元件應均勻分布,布置在通風良好的地方。散熱位置pcb設計兩,方便貼面和整機散熱。
(6)強信號和弱信號,高壓信號和弱電壓信號要完全分開;模擬信號和數字信號要分開;高頻信號和低頻信號要分開信號;高頻分量的分離應該是足夠的。
(7)熱容量大的元件布置不要太集中,以免局部溫度低導致焊接不良。
(8)對于電位器、可調電感等可調元件的布局,要考慮整機的結構要求,如果在機內調整,應放在PCB的頂部,方便調節;如在機外調節,其位置應與底盤面板上調節旋鈕的位置相適應。
(9)元器件的布置要方便調試和維護,QFP、BGA、PLCC等元器件周圍要有一定的維護空間。
(10)不要將高大、昂貴的元件放置在PCB邊緣或靠近插件、安裝孔、插槽和V-CUT等應力集中區域,以減少裂紋或裂紋。
(11) 需要考慮插座、連接器等部件之間是否存在干擾,是否與結構設計相矛盾。
(12)同類型插件組件應在X或Y方向的一個方向放置。同類型的極化插件組件在X或Y方向盡量保持一致可以方便生產和檢驗,同一塊板最多允許2個方向。
(13)焊接面的貼裝元件采用波峰焊生產工藝時,電阻和容器部分的長軸方向應與波峰焊的傳輸方向垂直,電阻和SOP(引腳間距≥1.27mm ) 元件長軸方向與波峰焊傳輸方向平行,間距為
QFP 器件應按 45 度方向排列,并添加偷來的焊盤。SOP等器件也應增加除錫焊盤。如下圖3.4b所示。較小的元件不應布置在較大的元件后面,以免較大的元件阻塞錫流并接觸較小元件的焊盤,導致漏錫。
(14)回流焊和波峰焊工藝限制元件布局。不同的SMT組裝工藝對元件布局有不同的要求。例如0402封裝的元件可以回流焊但不適合波峰焊。詳細請參考下表3-5。
PCB布局設計
布線就是按照原理圖和線表布置PCB線。接線的一般原則如下:
(1) 接線優先
密度優先原則:從PCB上最復雜的器件開始布線,從PCB上最密集的區域開始布線。
核心優先原則:例如DDR、RAM等核心部分應先布線,類似的信號傳輸線應提供專用層、電源和接地回路。其他次要信號應作為一個整體考慮,不應與關鍵信號發生沖突。
關鍵信號線優先布線原則:電源、模擬小信號、高速信號、時鐘信號、同步信號等關鍵信號優先布線。
布線層數的選擇原則:在滿足使用要求的前提下,布線的選擇順序是先單層布線,然后是雙層布線,最后是多層布線。
(2) 盡量為時鐘信號、高頻信號、敏感信號等關鍵信號提供專用布線層,保證最小的環路面積。人工優先布線,屏蔽,增加安全間距,確保信號質量。
(3)電源層和地層之間的EMC環境較差,避免放置對干擾敏感的信號。
(4)有阻抗控制要求的網絡應放在阻抗控制層,具有相同阻抗的差分網絡應使用相同的線寬和線距。時鐘線和高頻信號線應根據它們的特性阻抗要求 線寬以實現阻抗匹配。
(5) 輸入輸出端所用的線應盡量避免,線間最好加接地線,避免反饋耦合。
(6)數字地和模擬地要分開,低頻電路單點并聯接地;高頻電路多點串聯接地。數字電路,地線應閉合形成回路,提高抗噪能力。
(7)印制線的拐角一般是圓弧形的,直角或夾角會影響高頻電路中的電氣性能。
(8)接線轉折點一般為圓弧形,避免直角或直角,否則會影響高頻電路中的電氣性能。如圖3.6.
(9) 導線的最小寬度主要由導線與絕緣基板的粘合強度和流過它們的電流值決定。導線的最小間距主要由絕緣電阻和擊穿電壓決定在最壞的情況下,電線之間。
(10) 雙面板上的公共電源和地線盡量靠近板的邊緣,分布在板的兩側。多層板可以配電源和地線)內層的接地層,通過金屬化孔與各層的電源線和地線相連。
(1 當1)焊盤連接到較大的導電面積時,應使用長度不小于0.5mm的細線進行隔熱,細線的寬度不應小于小于 0.13mm。
(12)相鄰層的信號線正交以減少耦合。避免相鄰層對齊或平行走線。
PCB孔設計
PCB上常見的孔有安裝孔、定位孔、元件孔、過孔、盲埋孔、測試孔等。
(1) 洞)
安裝孔用于組裝器件或固定印制板。安裝孔應與安裝裝置的尺寸和公差相匹配。
(2) 洞)
定位孔是放置在電路板邊緣的非金屬化孔,用于電路板生產和組裝。詳見3.3。
(3) 洞
元件孔是用于將元件端子固定在印刷電路板上并電連接導電圖案的孔。元件孔的直徑應比安裝的元件引線直徑大0.2~0.3mm。
(4) 過孔)
過孔也稱為通孔,是用于內層連接的金屬化孔,但不用于插入元件引線或其他增強材料??讖酱笮『烷g距可根據布線間距的大小進行調整,一般孔徑為Φ0.3~Φ0.8mm,金屬化孔的電阻值不超過300μΩ。PCB的厚度決定了板子的最小過孔
(5) 盲孔和埋孔
盲孔是連接表層和內層但不穿透的過孔,埋孔是連接內層且表面看不到的過孔。在應用盲孔和埋孔設計時,應充分了解PCB加工工藝,避免PCB加工中出現不必要的問題,必要時與PCB供應商協商。
(6)測試孔(Test)
測試孔是指用于 ICT 測試目的的通孔。它們也可以用作通孔。原則上,孔徑不受限制。焊盤直徑不小于25mil,測試孔中心距不小于50mil。
可測試性設計
SMT測試包括在線測試(In-、ICT)和功能測試(-、FCT)。為了保證量產產品的質量,需要用到ICT和FCT,而SMT的可測性主要針對ICT。在PCB設計階段,必須考慮增加測試點。相關設計要求如下:
(1)測試點均勻分布在整個PCB板上。一般每個網絡至少要有一個測試點可以被測試探針接觸到。
(2)測試點選擇優先:圓形焊盤優先;其次器件引出引腳;最后一個過孔是最多的測試點。SMD器件最好使用圓形焊盤作為測試點,PCB帶有OSP加工工藝 不建議使用過孔作為測試點,當使用表面焊盤作為測試點時,測試點應盡可能放置在焊接面上。
(3)最小測試焊盤尺寸為0.6mm。當PCB空間較大時,測試焊盤設置為0.9mm以上。兩個獨立測試點的最小間距為1.5mm,推薦值為2.0mm,如圖3.8a。
(4)測試點不能被絲印覆蓋,絲印通過會出現接觸不良。測試點不能被條碼、膠帶等遮擋。
(5)測試點與SMD的距離至少1.25mm,測試點與IC器件的距離至少2.0mm,測試點與IC器件的距離至少為2.0mm測試點與DIP插件孔1.25mm,測試點與板邊的距離不小于5mm,如圖3.8b。
(6)添加測試點時,附加線盡量短。如圖3.8c。
(7)使用圓形焊盤作為測試點時,如果PCB表面處理工藝為OSP,建議在測試焊盤上印刷錫膏,以增強測試的可靠性。
(8)對于器件,如果引線較粗或Pitch≤1.5mm,測試點需要單獨引出。如圖3.8d。
(9)對于具有邊界掃描(-Scan)器件的VLSI和ASIC器件,應增加實現邊界掃描功能的輔助測試點,以滿足測試器件本身內部功能邏輯的要求。
免責聲明:部分文章信息來源于網絡以及網友投稿,本網站只負責對文章進行整理、排版、編輯,意為分享交流傳遞信息,并不意味著贊同其觀點或證實其內容的真實性,如本站文章和轉稿涉及版權等問題,請作者在及時聯系本站,我們會盡快和您對接處理。
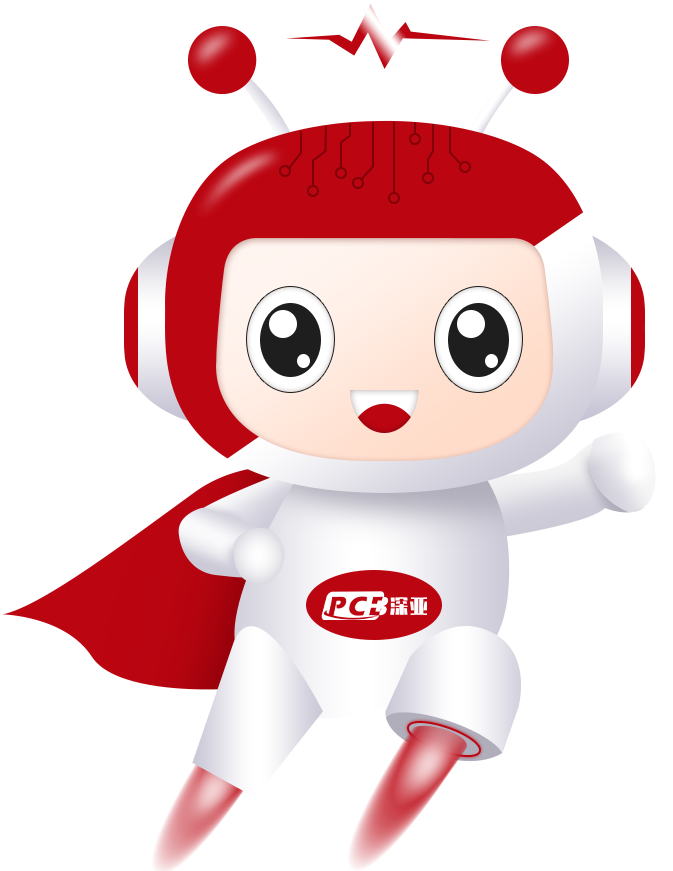